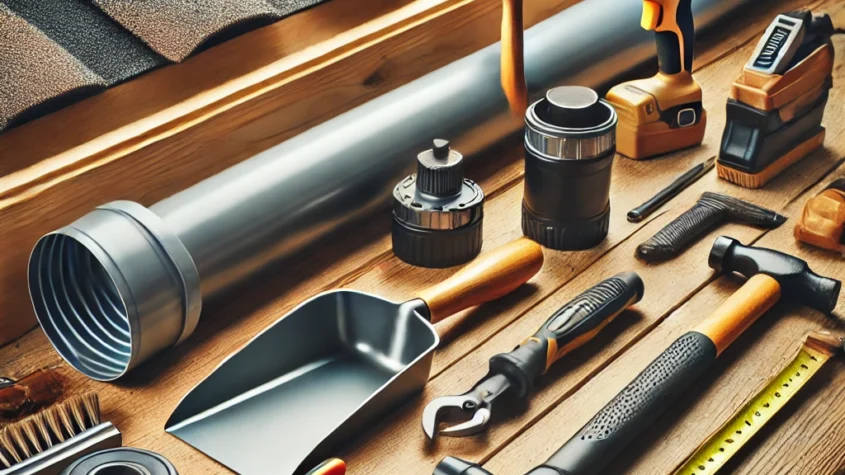
Perfect bending is a crucial technique in various fields, especially in manufacturing and design. It involves creating precise angles and curves in materials to achieve optimal functionality and aesthetic appeal. Mastering this process can significantly enhance the quality of finished products, making it essential for professionals and enthusiasts alike.
Achieving perfect bending requires a combination of the right tools, materials, and techniques. Factors such as material type, thickness, and bend radius play vital roles in determining the success of the bend. Understanding these aspects can help individuals streamline their approach, ensuring consistent and accurate results every time.
As technology evolves, innovative bending methods are emerging. These advancements not only improve precision but also increase efficiency, allowing for greater creativity in design. Exploring these developments offers valuable insights into achieving perfect bends that can elevate any project.
Essentials of Perfect Bending
Achieving perfect bending requires a thorough understanding of materials, the right tools, and effective bending techniques. Knowledge in these areas ensures precision and quality in the final product.
Materials and Alloy Properties
The choice of material significantly impacts the bending process. Common materials include steel, aluminum, and copper, each with specific properties.
- Steel: Offers high tensile strength but requires careful handling to avoid cracking.
- Aluminum: Lightweight and malleable, aluminum is ideal for complex shapes but is sensitive to stress.
- Copper: Known for its ductility, it bends easily when heated.
Alloy compositions also play a crucial role. Hardened alloys may be more challenging to bend, while softer alloys allow for greater flexibility. Understanding these properties helps in selecting the right material for the specific bending application.
Bending Techniques and Methods
Various bending techniques cater to specific materials and desired outcomes. Some common methods include:
- Air Bending: Uses a punch and die to form the material, allowing for adjustments post-bend.
- Bottom Bending: Provides a more defined angle through complete contact with the die.
- Rotary Bending: Involves rotating the part around a fixed point for complex shapes.
Each technique requires knowledge of material properties, as different techniques yield varying results based on the hardness and thickness of the material. Selecting the appropriate method ensures precision and reduces the risk of defects.
Tooling and Equipment Essentials
Proper tooling is vital for achieving perfect bends. The following tools are essential:
- Bending Press: Provides consistent force and control, crucial for accurate bends.
- Dies and Punches: Customized shapes help achieve desired angles and radii. It’s essential that they are compatible with the material and method.
- Mandrels: Support the material during bending, especially for tubes or pipes.
Ensuring tools are well-maintained and appropriate for the specific task boosts efficiency and quality. Selection of the right equipment influences the bending process, making it a critical step in achieving precise results.
Application of Bending Skills
Bending skills find diverse applications across various industries and practical scenarios, optimizing performance and enhancing productivity. Mastering these techniques is essential for efficiency and precision in multiple fields.
Industrial Applications
Bending skills are critical in manufacturing, particularly in metal fabrication. Techniques such as press braking and tube bending are widely used to shape materials according to design specifications.
- Aerospace: Companies moldaluminum and titanium for aircraft components, ensuring strength and weight efficiency.
- Automotive: Bending enables the creation of chassis and exhaust systems, focusing on durability and performance.
- Construction: Steel bending is essential for structural reinforcements in buildings and bridges.
Understanding the machinery and tools used, such as CNC machines, increases production capabilities and enhances product quality.
Practical Tips for Efficient Bending
Efficiency in bending requires a focus on both technique and tool selection. Proper planning can significantly reduce waste and errors.
- Choose the Right Tool: Select tools based on material type and thickness. Hydraulic or electric presses greatly influence the outcome.
- Calculate Angles Precisely: Use templates or software for accurate measurements to avoid costly mistakes.
- Maintain Equipment: Regular maintenance of bending machines ensures reliability and longevity, preventing breakdowns during critical operations.
Implementing these strategies can streamline processes and improve outcomes in projects involving bending techniques.
Rent Mini Excavator Near Me: Your Guide to Affordable Options and Local Availability
Renting a mini excavator can be a game changer for small construction projects, landscapin…